Restoring the Floor in Your Vintage Trailer: Step-by-Step
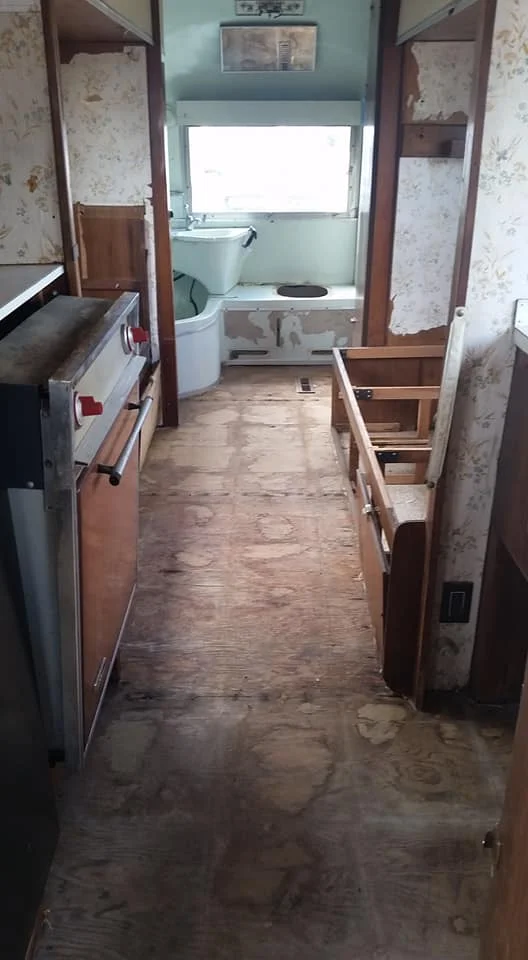
One of the most common and challenging issues vintage trailer owners face is floor rot. Decades of undetected water leaks, often around windows, vents, or seams, can lead to significant damage to the subfloor. A soft, bouncy, or discolored floor isn’t just an eyesore; it compromises the structural integrity of your trailer and can be a safety hazard.
Restoring the floor in your vintage trailer is a big project. It requires patience, effort, and attention to detail. However, it’s also incredibly rewarding to replace damaged sections with a solid, new foundation. This guide will walk you through the process, step by step, to help you understand what’s involved.
While this guide provides a detailed look at the process, the complexity of floor restoration can vary greatly depending on the extent of the damage and the specific model of your vintage trailer. If you’re unsure about tackling this project yourself or the damage is extensive, know that American Vintage Trailers specializes in expert vintage trailer floor restoration.
Let’s start by understanding when this kind of work is necessary.
When is Floor Restoration Needed? Identifying the Problem
So, how do you know if your vintage trailer’s floor needs attention beyond a simple cleaning or covering? Your trailer will likely show you the signs if you look and feel carefully.
- Soft or Spongy Spots: This is the most classic sign. When you walk across the floor, do certain areas feel soft, spongy, or like they’re giving way under your weight? This indicates the underlying subfloor has likely been compromised by water and is rotting.
- Visible Discoloration or Stains: Look for dark stains, discoloration, or water marks on the flooring material itself, especially near walls, windows, or plumbing fixtures. These stains are often evidence of past or ongoing water intrusion that has affected the subfloor.
- Musty or Moldy Odors: A persistent musty or moldy smell inside your trailer, even after cleaning, is a strong indicator of mold or mildew growth, which thrives in damp environments caused by water damage to the subfloor and surrounding structures.
- Bowing or Unevenness: In some cases, severe water damage can cause the subfloor to bow, warp, or become noticeably uneven.
- Visible Decay: In advanced stages, you might even see visible signs of rot or disintegration in the subfloor material around edges or where the finished flooring is missing.
The Root Cause: Almost without exception, floor rot in a vintage trailer is caused by water intrusion. The water seeps in through failed seals (windows, doors, roof vents, body seams) or plumbing leaks and gets trapped, allowing the wood subfloor to rot.
Identifying these signs early is crucial. The sooner you address floor rot and, importantly, the water source causing it, the less extensive and costly the repair will be.
Gather Your Tools and Materials
Before you start pulling up that old, rotten floor, take the time to gather all the necessary tools and materials. Having everything on hand will prevent frustrating delays once you’ve started the demolition.
Safety Gear (Non-Negotiable!):
- Safety Glasses: Protect your eyes from flying debris, dust, and rust.
- Heavy-Duty Gloves: Protect your hands from splinters, sharp edges, and tools.
- Dust Mask or Respirator: You’ll be dealing with old insulation, dust, and potentially mold spores. Protect your lungs.
- Hearing Protection: If using power tools like saws.
- Work Boots: Protect your feet.
Demolition Tools:
- Pry Bar: For lifting and prying up old flooring and subfloor sections.
- Hammer: For general prying and demolition.
- Reciprocating Saw: A powerful tool for cutting through stubborn sections of plywood, screws, and sometimes even small metal bits. Have blades suitable for both wood and metal.
- Utility Knife: For cutting finished flooring materials and getting into tight spots.
- Shovels and Buckets: For scooping and carrying away debris.
Cleaning Supplies:
- Heavy-Duty Cleaner/Degreaser: For cleaning the exposed frame and any salvageable areas.
- Scrub Brushes: For cleaning rust or grime from the frame.
- Shop Vacuum: Essential for cleaning up dust, debris, and insulation effectively.
Repair Materials:
- New Plywood: You’ll need exterior-grade plywood of the appropriate thickness to match your original subfloor (often 1/2 inch or 5/8 inch). Get enough to cover the damaged area, plus a little extra.
- Fasteners: Screws or bolts of appropriate size and type to secure the new plywood to your trailer’s frame members (steel or aluminum). Use fasteners compatible with the frame material to prevent corrosion.
- Wood Treatment/Sealant: Consider sealing the edges of the new plywood with a wood treatment or sealant to add an extra layer of protection against moisture.
- Metal Primer and Paint: If you find and clean rust on your steel frame, you’ll need primer and paint suitable for metal to protect it.
- Sealants: Appropriate sealants for sealing the edges of the new subfloor to the exterior walls or frame (use a sealant compatible with your exterior skin material).
Measuring and Cutting Tools:
- Measuring Tape: For accurate measurements of the areas to be replaced and the new plywood.
- Straight Edge: For marking straight lines on the plywood.
- Circular Saw or Jigsaw: For cutting the new plywood to size. A circular saw is good for straight cuts, while a jigsaw is useful for curved or irregular shapes.
- Drill and Appropriate Bits: For drilling pilot holes and driving screws.
Optional but Recommended:
- Jumper or Bracing Material: If you need to temporarily support the trailer body or frame sections during demolition.
- Extra Lumber: For temporary supports or patching small areas.
Pro Tip: Take photos as you go, especially during demolition. This can be a valuable reference when it comes time to reinstall components or figure out how things were originally put together.
Gathering all these items before you begin will save you trips to the store and help the restoration process flow more smoothly.
Step 1: Preparation and Safety First
Before you even think about cutting into your vintage trailer’s floor, you need to prepare the space and ensure you’re working safely. This is crucial for both the success of the project and your well-being.
- Empty the Trailer Completely: Remove absolutely everything from the interior of your vintage trailer. This includes furniture, cushions, personal items, and anything stored inside. You need a clear workspace to access the floor.
- Disconnect Utilities: Safety is paramount! Disconnect your trailer from any shore power connection. Turn off and disconnect your propane tanks. If you have solar panels, follow the proper procedure to safely disconnect them as well.
- Wear Appropriate Safety Gear: Put on your safety glasses to protect your eyes from debris. Wear heavy-duty gloves to protect your hands. Use a dust mask or respirator to avoid inhaling dust, old insulation fibers, and potential mold spores. If you plan to use power tools, put on your hearing protection.
- Ventilate the Workspace: Open windows and doors to ensure good airflow. This helps with dust control and provides ventilation if you’re dealing with mold or old materials.
- Clear the Immediate Area Around the Trailer: Make sure the area outside your trailer is also clear of obstacles, debris, or anything you could trip over. You’ll be moving in and out frequently.
Safety is Not Optional: Taking shortcuts on safety can lead to injuries. Always wear your protective gear throughout the demolition and restoration process.
Getting the trailer emptied and ensuring all utilities are safely disconnected are essential preliminary steps. With the workspace prepared and your safety gear on, you’re ready for the next critical step – addressing the source of the problem.
Why Choose Us
For Your Restoration?
- 13+ years of experience in vintage trailer repairs, remodels, and restorations
- 40+ years of electrical and mechanical experience
- Expert craftsmanship with high-quality materials
- Located in the heart of Texas
- Serving Airstream and RV owners across Texas – from DFW to Austin, Texas Hill Country, Brazos Valley, and beyond!
- Custom solutions for modern and classic RVs
Ready to restore your vintage trailer?
Call us today for a quote!
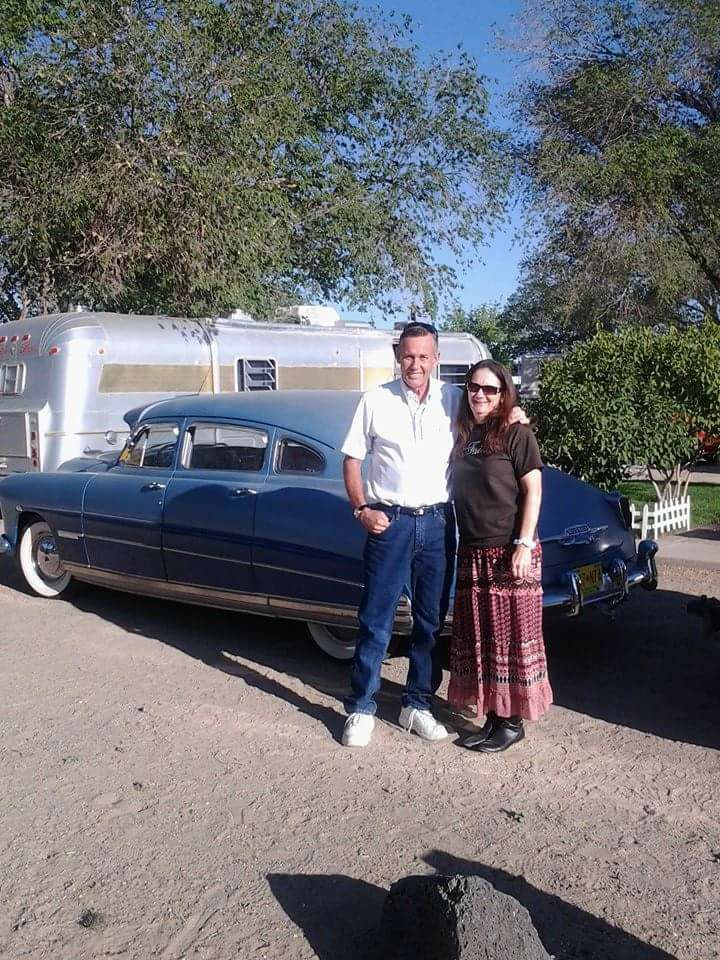
Step 2: Find and Fix the Water Source (CRITICAL!)
You might be eager to start ripping out that rotten wood, but hold on! Repairing or replacing your vintage trailer’s floor without first finding and permanently fixing the water leak that caused the damage is a fundamental mistake. It’s like mopping up a flooded bathroom without turning off the leaky faucet – the problem will just keep coming back, ruining your new floor.
Why is fixing the water source so crucial?
- Preventing Future Rot: If the leak isn’t stopped, water will continue to seep in and damage your brand new subfloor. Your hard work and financial investment will be wasted.
- Addressing the Root Problem: The rotten floor is a symptom, not the disease. You have to cure the disease (the water leak) to truly restore your trailer’s integrity.
- Avoiding Escalating Damage: Ongoing leaks can continue to damage other areas of your trailer, including walls, insulation, and frame components.
How to find the water source:
- Inspect All Exterior Seals: Carefully examine the seals around every window, door, roof vent, skylight, antenna, and access hatch. Look for cracks, gaps, dryness, or areas where the sealant is pulling away from the trailer’s skin or the component it’s sealing. These are the most common entry points for water.
- Check Body Seams: Inspect the seams where body panels join, especially on the roof and sides, and around wheel wells. Old sealant in these areas can fail.
- Look at Plumbing Penetrations: Check where water pipes, drain lines, or holding tank vents exit the trailer through the floor or walls. Seals around these penetrations can fail.
- Consider the Belly Pan: Sometimes, water can enter from below if the belly pan (the enclosure under the trailer) is damaged or has failing seals around its edges or access points.
- Water Testing: A controlled water test can help pinpoint stubborn leaks. With someone inside the trailer, have another person slowly and carefully spray water from a hose on small sections of the exterior (e.g., one window at a time, a specific roof vent). Observe carefully inside for any signs of water entering.
Take Your Time Here: This step requires patience and a meticulous eye. Don’t rush it. If you’re having trouble finding the leak, consider seeking assistance from someone experienced in vintage trailer water leak repair. Fixing the leak properly often involves removing old sealant completely and applying new, appropriate sealant specific to your trailer’s materials.
Once you are absolutely confident that all water leaks have been found and permanently repaired using the correct methods and materials, you can finally move on to the demolition phase.
Step 3: Demolition - Removing the Old Floor
This step requires careful work to remove the rotten sections of the subfloor while minimizing damage to the rest of your vintage trailer.
- Identify the Damaged Area: Clearly mark the sections of the floor that are soft, discolored, or show other signs of water damage and rot. Extend your marked area slightly into what appears to be sound wood, as damage can sometimes spread beyond the visible signs.
- Remove Covering Materials: Carefully remove any finished flooring material (carpet, vinyl, tile, etc.) from the marked area. Use your utility knife or scraper to help lift it. Be prepared for adhesive that might be holding it down.
- Work Around Obstacles: You’ll likely encounter interior walls, cabinets, appliances, or plumbing/electrical lines running through the floor.
- Carefully Remove or Work Around: If possible, try to work around fixed obstacles by cutting the subfloor neatly around them. If components are over a large damaged area, you might need to carefully disconnect and remove them for better access. Take photos before disconnecting anything to help with reinstallation.
- Watch for Utilities: Be extremely cautious of any electrical wires or plumbing pipes embedded in or running under the subfloor. Know where your utility lines are located before you cut or pry aggressively.
- Cut Out Damaged Sections: Using your circular saw or jigsaw, carefully cut out the marked sections of the rotten plywood.
- Cut Close to Frame: Aim to make your cuts directly over or very close to the underlying frame members (joists or crossmembers) where the subfloor is attached. This gives you a solid point to attach the new plywood later.
- Set Saw Depth: Adjust the depth of your saw blade so it cuts only through the subfloor plywood and doesn’t cut into the frame members or anything below the belly pan.
- Pry Up Carefully: Once sections are cut, use your pry bar and hammer to carefully lift and remove the rotten plywood pieces. They might be stuck to the frame with old fasteners or adhesive.
- Remove All Debris: As you remove sections of the old floor, scoop or shovel the debris into buckets and take it outside for disposal.
- Inspect Edges of Remaining Subfloor: Once the damaged sections are out, inspect the edges of the remaining original subfloor. If you see any signs of discoloration or softness at the edges, extend your cuts to remove all compromised wood.
Demolition is a process, not a race. Take your time to avoid accidentally cutting into wires, pipes, or damaging the frame or surrounding interior components.
With the old, rotten floor sections removed, you’ve exposed the foundation of your vintage trailer. Now it’s time to clean and inspect what’s underneath.
Step 4: Cleaning and Assessment
Now that the rotten wood is out of the way, you have a clear view of the trailer’s frame and any remaining original subfloor. This step is essential for preparing for the new floor and identifying any underlying issues with the frame itself.
- Thoroughly Clean the Exposed Area: Use your shop vacuum to meticulously clean the entire exposed frame area. Remove all sawdust, dirt, debris, and any lingering pieces of rotted wood or insulation. Get into all the nooks and crannies of the frame members.
- Scrape Away Any Residue: Use a scraper or wire brush to remove any stubborn adhesive residue, old sealant, or loose rust from the top surfaces of the frame members where the subfloor attaches. A clean surface is important for the new subfloor to sit flat and secure.
- Inspect the Frame for Rust: Carefully examine the entire length of the exposed frame for signs of rust and corrosion. Pay close attention to areas around wheel wells, outriggers (the pieces extending from the main frame rails to the sides of the body), and crossmembers.
- Look for Cracks or Bending: Inspect the frame members for any cracks, bends, or signs of fatigue. This is particularly important around suspension mounting points and areas that might have experienced impacts. Use a bright light to help spot fine cracks.
- Assess the Condition of Remaining Subfloor: If you only removed sections of the subfloor, carefully inspect the edges and surface of the remaining original subfloor to ensure it is solid and free of any lingering rot or damage.
Don’t Rush This Inspection: Take your time to thoroughly assess the condition of your trailer’s frame. Finding and addressing frame issues now, while the floor is open, is significantly easier (and less expensive) than doing it later.
Identifying any problems with the frame during this stage is crucial. If you find significant rust, cracks, or bending, you may need to address those issues before installing the new subfloor.
Step 5: Repairing/Treating the Frame (If Needed)
With the subfloor removed, you have a clear view of your vintage trailer’s frame. This is the perfect opportunity to inspect it and address any issues you found during the cleaning and assessment phase (Step 4). The most common problems are rust on steel frames and, less often, cracks or bending.
Address Rust (Steel Frames): If your vintage trailer has a steel frame and you found areas of rust (which is very likely!), now is the time to treat it.
- Remove Rust: Use a wire brush, grinder with a wire wheel, or sandpaper to thoroughly remove all loose and surface rust. Get down to bare metal if possible.
- Apply Rust Inhibitor: Once the rust is removed and the area is clean, apply a quality rust-inhibiting primer or converter to the affected areas. Follow the product instructions for application and drying time.
- Paint the Frame: After the primer is dry, paint the frame members with a durable metal paint suitable for exterior use. This will help protect the steel from future corrosion.
Address Cracks or Bending (Likely Requires Professional Help): If you found any cracks in the frame members or evidence of bending or warping, this is typically not a DIY repair.
- Assess the Severity: Try to understand the extent of the crack or bend.
- Do Not Proceed with Floor Installation: Installing a new subfloor over a compromised frame is dangerous and will not fix the underlying structural issue. The frame must be repaired first.
- Consult a Professional: Frame repair, especially involving welding (which requires specific skills and equipment) or straightening bent sections, is best left to experienced professionals who understand vintage trailer construction and frame dynamics.
Listen to Your Frame: The frame is your trailer’s foundation. While you can tackle basic rust treatment yourself, any cracks, significant material loss due to rust, or bending means the frame’s structural integrity is compromised. This requires professional attention to ensure your safety.
Addressing frame issues now, while the subfloor is removed and the frame is exposed, is much easier and more cost-effective than trying to fix it later.
If you’ve found significant frame damage that’s beyond simple rust treatment, American Vintage Trailers has the expertise in vintage trailer frame repair to ensure your foundation is safe and sound before you lay the new floor.
Once you’ve addressed any necessary frame repairs or treatment, you’re ready to start putting in the new subfloor.
Step 6: Measuring and Cutting New Subfloor
Getting the new subfloor pieces cut accurately is essential for a solid and well-fitting floor. Take your time with your measurements and cuts.
Measure the Opening(s): Carefully measure the dimensions of the open area(s) where you removed the rotten subfloor. Measure the length and width precisely. If the opening is irregular, take multiple measurements to capture its shape accurately.
- Measure Existing Plywood Edges: If you cut the old subfloor back to a solid edge of existing plywood, measure from that edge to the nearest frame member where the new piece will be supported.
Use Old Pieces as Templates (If Possible): If the pieces of old subfloor you removed are still intact enough and haven’t warped or shrunk significantly, you can sometimes use them as templates for cutting the new plywood. Lay the old piece on top of your new plywood sheet and carefully trace its shape.
- Inspect the Template: Make sure the old piece is still the correct shape before using it as a template, especially if it was severely water-damaged.
Transfer Measurements to New Plywood: If you’re measuring the opening directly, transfer those measurements to your new plywood sheets. Use a measuring tape, straight edge, and a pencil or marker to mark your cut lines clearly.
- Double-Check Everything: Before you make any cuts, double-check all your measurements and transfer marks. “Measure twice, cut once” is a crucial rule here!
Plan Your Seams: If you need to use multiple pieces of plywood to fill a large area, plan where your seams will fall.
- Support Seams: Always aim to have plywood seams land directly over a frame member (a joist or crossmember). This provides crucial support for the edges of the plywood and prevents weak spots in your new floor. Avoid having seams hang unsupported between frame members.
- Stagger Seams: If you’re replacing a large area, try to stagger the seams of adjacent plywood sheets (like brickwork) rather than having all seams line up in a single line. This can add strength to the overall floor.
Cut the New Plywood: Using your circular saw (for straight cuts) or jigsaw (for irregular shapes or curves), carefully cut the new plywood sections along your marked lines.
- Cut Outdoors if Possible: Cutting plywood creates a lot of sawdust. Doing this outdoors or in a well-ventilated area is recommended.
- Use a Sharp Blade: A sharp saw blade will make cleaner cuts and be easier to work with.
Patience Pays Off: Taking the time to measure and cut accurately will save you headaches during installation. Snugly fitting pieces create a stronger and more professional-looking repair.
With your new subfloor pieces cut to size, you’re ready for the rewarding step of installing them into your trailer.
Step 7: Installing the New Subfloor
Carefully fitting and securing the new plywood sections is essential for a solid and durable floor in your vintage trailer. Take your time to ensure each piece is properly seated and fastened.
- Position the First Piece: Take one of your cut plywood sections and carefully position it in the opening in the floor. Ensure it fits snugly against the frame members and any remaining original subfloor.
- Ensure Proper Alignment: If you are installing multiple pieces, make sure the edges that will form a seam are properly aligned over a frame member for support.
- Secure the Plywood to the Frame: Using your drill and the appropriate fasteners (screws or bolts compatible with your frame material – steel or aluminum), begin securing the plywood to the underlying frame members.
- Start at Corners: It’s often helpful to start by fastening the corners of the plywood piece to hold it in place.
- Fasten Along Frame Members: Drive fasteners along the length of every frame member that the plywood crosses. Space the fasteners evenly (e.g., every 6-8 inches).
- Avoid Overtightening: Be careful not to overtighten the fasteners, as this can strip the wood or even damage the frame. Just make them snug enough to hold the plywood firmly in place.
- Install Additional Pieces: If you have multiple sections of plywood to install, position the next piece and secure it to the frame members, ensuring the seam aligns properly over a frame member if necessary.
- Address Any Small Gaps: If there are very small gaps where the new plywood meets the original subfloor or the frame, these will typically be addressed in the next step with sealant. Large gaps might indicate a measuring or cutting error.
Listen to Your Drill: When driving screws, listen for the sound of the screw biting into the frame. If you’re working with a steel frame, you’ll likely be using self-tapping screws designed for metal. For aluminum frames, you’ll use different fasteners and potentially pre-drilled holes.
A securely fastened subfloor is the foundation for your finished flooring and contributes significantly to the overall rigidity of your trailer.
Step 8: Seal the Edges of the New Floor
Properly sealing the edges of your newly installed subfloor is absolutely crucial for preventing future water intrusion. This step creates a barrier where the plywood meets the trailer’s exterior walls and frame.
- Choose the Right Sealant: Select a high-quality sealant that is specifically recommended for RV use and is compatible with the materials of your trailer’s exterior skin (aluminum, fiberglass, etc.) and the plywood subfloor. Avoid standard household sealants that may not hold up to the movement and weather exposure of an RV.
- Prepare the Area for Sealant: Ensure the edges where the plywood meets the frame or wall are clean and dry. If necessary, use a vacuum or brush to remove any lingering dust or debris.
- Apply the Sealant: Using a caulk gun, apply a continuous bead of sealant into the gap where the edge of the new plywood meets the trailer’s structure.
- Ensure Full Coverage: Make sure the sealant completely fills the gap and creates a solid seal.
- Focus on the Perimeter: Pay special attention to the edges along the exterior walls of the trailer, as these are primary points of water entry.
- Consider Underside Sealing: Some restorers also recommend sealing the underside edges of the plywood where it sits on the frame members before the belly pan is reinstalled. This adds another layer of protection.
- Smooth the Sealant (Optional): For a neater appearance and to ensure good contact, you can gently smooth the bead of sealant with a gloved finger or a sealant-smoothing tool.
- Allow Sealant to Cure: Let the sealant cure fully according to the manufacturer’s instructions before proceeding with the next steps. This ensures a strong and watertight bond.
Don’t Skip or Rush This Step: The quality of the seal here is vital for the longevity of your new floor. A poor seal means water can get back in, and you’ll be dealing with rot again down the road.
A properly sealed subfloor creates a strong defense against future water damage.
Step 9: Reinstall Interior Components &
Step 10: Install Finished Flooring
Depending on the layout of your trailer, you’ll need to reinstall and hook up any parts you removed to access the subfloor. Then you’ll install the finished flooring.
- Reinstall Interior Components:
- Appliances, Cabinets, or Walls: Carefully reinstall any appliances, cabinetry, or interior wall sections you had to remove for access to the subfloor. Ensure they are secured in their original positions and properly attached to the floor and walls.
- Plumbing & Electrical: Reconnect any plumbing lines, electrical wiring, or propane lines you disconnected. Important: When working with gas lines, be extremely cautious and double-check all connections for leaks. Test electrical connections for proper function before closing up walls or cabinets.
- Install Finished Flooring:
- Prepare the Subfloor: Ensure the new subfloor is clean and free of any debris.
- Choose Flooring: Most people install vinyl, but other kinds of flooring work too, such as carpet, laminate, or tile.
- Install Flooring Material: If you’re going with vinyl, unroll it and ensure it’s flat. Trim it to fit and glue it down with the recommended adhesive. With other materials, follow any instructions included with the product.
- Secure Edges: Install any trim pieces along the edges of the floor where it meets the walls or cabinets.
Patience and Precision: With electrical and plumbing, be deliberate to ensure proper hookups. Taking care here prevents major headaches and safety hazards.
With these parts reinstalled and the floor looking like new, you’re near the end of your floor restoration project! Just be sure to address any leaks.
DIY vs. Professional Floor Restoration: Knowing When to Call the Experts
Restoring the floor in your vintage trailer, as you can see from the steps, is a significant undertaking. For some vintage trailer owners, it’s a rewarding DIY project that saves money on labor. However, for others, the complexity, the extent of the damage, or the need for specialized skills means that professional help is the better route. Knowing when to call in the experts can actually save you money and headaches in the long run by ensuring the job is done correctly the first time.
When might tackling floor restoration yourself be a viable option?
- Limited, Accessible Damage: If the floor rot is confined to a small, easily accessible area (like near a doorway or a single window) and doesn’t involve structural frame damage, a skilled and prepared DIYer might be able to cut out and replace that section.
- Comfort with Tools and Process: If you are comfortable using power tools (saws, drills), understanding measurements, and following a step-by-step process carefully, you might have the basic skills needed.
- Time and Patience: DIY floor restoration takes time. If you have the patience and dedication to work through the steps meticulously, you can potentially save on labor costs.
When is calling in professional help often the more practical (and potentially more budget-friendly) decision?
- Extensive Floor Rot: If a large portion of the subfloor is damaged, or if the rot extends under walls, cabinets, or appliances that are difficult to remove, the complexity and labor involved increase dramatically.
- Involvement of Frame Damage: If, after removing the subfloor, you discover significant rust, cracks, or bending in the frame, this requires specialized frame repair skills and equipment that most DIYers don’t possess. Attempting frame repair yourself is dangerous and will likely require professional correction later.
- Complexity of Layout: Vintage trailers with complex interior layouts, integrated cabinets, or embedded systems in the floor might make accessing and replacing the subfloor very challenging.
- Uncertainty About Water Source: If you cannot definitively find and fix the source of the water leak in Step 2, a professional can assist with thorough leak detection. Replacing the floor without fixing the leak guarantees the problem will return.
- Ensuring Structural Integrity and Safety: A properly restored floor is crucial for the overall structural integrity and safety of your trailer. If you’re unsure about any part of the process or concerned about getting it absolutely right, professional expertise provides peace of mind and prevents potential future issues.
The Cost of Fixing Mistakes: Attempting a complex floor restoration yourself and making errors (like not fixing the leak, damaging the frame, using incorrect materials, or improper sealing) can lead to the need for professional repair anyway – and fixing DIY mistakes is almost always more expensive than having a professional do the job correctly from the start.
Assessing the extent of the damage honestly and being realistic about your own skills and the complexity of the project is key. For many vintage trailer owners, especially when facing significant floor rot, professional restoration services are a wise investment that ensures a safe, durable, and properly repaired floor.
At American Vintage Trailers, we have extensive experience in vintage trailer floor restoration, from addressing minor soft spots to complete subfloor replacements. Our skilled team understands the nuances of various vintage trailer constructions and can provide expert repairs that stand the test of time, ensuring your trailer’s foundation is solid.
A Solid Foundation for Future Adventures
Restoring the floor in your vintage trailer is undoubtedly a significant undertaking. It requires careful planning, diligent work, and a commitment to doing it right. However, the effort is well worth it. Replacing rotten subfloor ensures the structural integrity of your trailer, provides a safe and solid surface underfoot, and stops the spread of damage caused by water intrusion.
Remember, the most crucial step is always finding and permanently fixing the water leak that caused the damage in the first place. Installing a new floor over an active leak is a recipe for repeated failure and wasted expense. Be thorough in your leak detection and repair before laying any new plywood.
While this step-by-step guide provides a detailed roadmap, the reality of vintage trailer restoration means that individual projects can vary greatly in complexity. The extent of the damage, the specific model of your trailer, and any unexpected issues encountered along the way can all influence the process.
If the floor rot in your vintage trailer is extensive, involves underlying frame damage, or if you simply prefer to have this critical repair handled by experienced professionals, American Vintage Trailers is here to help. Our skilled team specializes in vintage trailer floor restoration and understands the nuances of various vintage constructions. We can accurately assess the damage, address any underlying issues, and perform high-quality repairs to ensure your trailer has a solid foundation for many more adventures.
Ready to get expert help with restoring your vintage trailer’s floor?
Contact American Vintage Trailers today by calling 254-248-1186 (click to call if using a mobile device) to schedule your vintage trailer repair, restoration, or remodel.
Build your vintage trailer dream on a solid foundation!